What is a PCB and PCB Design? Altium
Table Of Content

It would be best if you tried to space components out where possible, allowing for direct access to the critical nodes. This is to ensure the copper wiring can reach all parts of the PCB comfortably. It also avoids any chance that your PCB short-circuits due to traces connecting because they were too close to each other. The main component packaging type that can drive the use of HDI design and manufacturing in a PCB build is ball grid array (BGA) packaging, as well as related packaging types like land grid array (LGA). Many popular microcontrollers, MPUs, and FPGAs are offered in BGA packaging as this is the easiest way to fit a large number of I/O pins into a small component package size.
The PCB Design Process
The beginning piece of a PCB is almost always the base substrate material. As mentioned in the introduction, this is usually FR-4 fiberglass sheeting. Using a solid core material like fiberglass is what gives PCBs their rigidity and helps prevent damage like accidental snapping. However, there are also flexible PCBs — used in items that require electronics to curve — that are built out of flexible plastic that is also capable of resisting high temperatures. The most common type of substrate sheeting in use today is FR-4 — flame retardant, grade 4 — glass-reinforced epoxy laminate sheeting.
Try Altium Designer
Magna Electronics Technology, Inc. specializes in products for the automotive industry. Its 600 employees can design entire vehicles at this Holly, MI, location. The drill removes a small amount of copper each time it moves across the board. This method is cheaper per board, but the equipment to make it is expensive. This method is not used often, because the other two methods are easier.
Drop Those Components Like It’s Hot
This includes determining the size, shape, and number of layers required, as well as the types of components that will be used. Once these requirements are established, the designer can move on to the next step. With the components placed (although they can be moved as needed), it is time to connect the nets. This is done by converting the rubber-band net connections into drawn traces and planes.
Data and Statistics on the U.S. Printed Circuit Board Industry
A. The choice of PCB material depends on factors such as the operating environment, frequency, and power requirements of the application. FR-4 is a common material for general-purpose PCBs, while high-frequency laminates or metal-core substrates may be used for more specialized applications. In addition to component symbols, schematics also use various types of connectors and labels to indicate how different parts of the circuit are interconnected. Power and ground symbols, for instance, are used to show the connection to the power supply and ground planes, while port symbols are used to represent external connections to the PCB. PCB design has evolved from the early days of sticky back component patterns and tape placed on a mylar sheet that was then photographed to create a production tooling master artwork used for manufacturing. With the evolution in PCB design over the decades, the process, and individual roles of the key stakeholders of who does what, and when within the design process has evolved as well.
Step 1: Schematic Capture
This may involve using thermal vias, heat sinks, or other cooling techniques to prevent overheating and ensure reliable operation of the circuit. The Joint Electron Device Engineering Council (JEDEC) publishes thermal management standards for various electronic components. [2] Following these standards ensures proper thermal performance and component longevity during placement. Also note whether you'll be using any differential pair routing in the design. The impedance solver in the Layer Stack Manager enables differential pair solutions as well as single-ended, so you can determine both requirements and use these when routing.
Today’s designer must address 3 perspectives for success, with the goal of making the first iteration work as intended. With such diverse key stake holders being both internal and external, organized complexity demands multi-discipline collaboration and integration. Refer to Figure 2 for an example of today’s system level connectivity – organizational complexity.
Impedance Matching and Termination
Solder mask is used by the manufacturers to keep the copper tracks and pads insulated from other metal, pieces of solder or other pieces of conductive material. A. Proper impedance matching can be achieved by controlling the geometry of the traces (e.g., width, spacing) and the properties of the dielectric material. Specialized tools and calculators are available to help designers determine the optimal trace geometry for a given impedance. A. Multi-layer PCBs offer several benefits, including increased routing density, better signal integrity, and improved EMI/EMC performance.
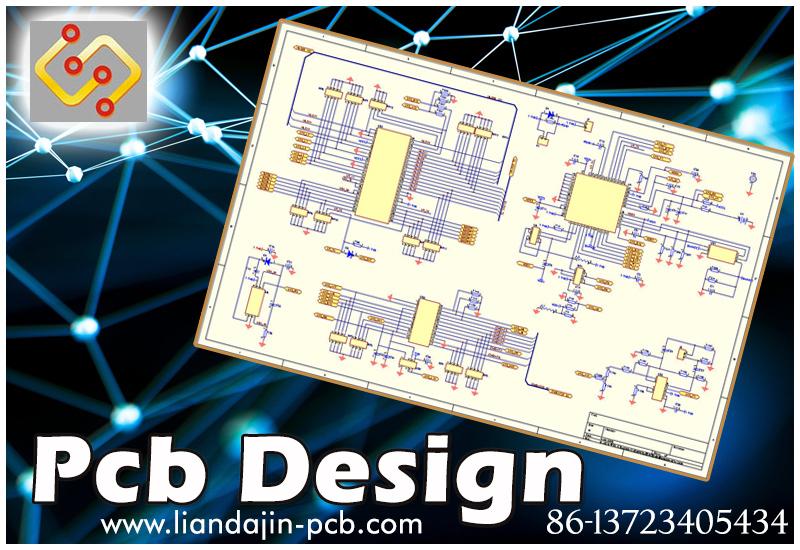
Create the Schematic
Although the production processes are very different, the process for designing UHDI PCBs is very similar to that for conventional PCBs. Integrated 3D modeling for printed circuit board design makes Altium Designer stand out from the rest. Managing this process is daunting, but a circuit board design application like Altium Designer can help guide you through the process. When you know what to look for in your layout, you can spot when you’ve made mistakes and can quickly correct them before you finish your circuit board.
The thickness of the copper used in PCB manufacture tends to vary by manufacturer or use, but it is generally specified in ounces per square foot. All files created by LibrePCB arehuman-readable, canonical and conceived very carefully.This allows to use version control systems on libraries and projects withoutstruggling with unintended or obfuscated diffs. The following overview describes what are the core knowledge and competencies to best serve in the role of Printed Circuit Engineering Layout as a stand-alone professional, or as the engineer performing this responsibility.
Miniaturization, Major Innovations Help Map the Course of Next-Gen PCBs - DuPont
Miniaturization, Major Innovations Help Map the Course of Next-Gen PCBs.
Posted: Wed, 07 Feb 2024 08:00:00 GMT [source]
The most common type of printed circuit board, the double-sided board, has two layers of copper foil, one on each side. So a 16-layer PCB is made up of eight double-layer boards, each with two pieces of copper sheeting, one per side. This step involves placing components and routing traces on the board to create a physical representation of the circuit. The layout process must take into account various design rules, such as minimum trace widths, clearances, and via sizes, to ensure manufacturability and reliability.
A broader perspective on PCB design - Engineer Live
A broader perspective on PCB design.
Posted: Mon, 23 Oct 2023 07:00:00 GMT [source]
Phenolics have a low thermal decomposition temperature which causes them to delaminate, smoke and char when the soldering iron is held too long on the board. As electronics moved from vacuum tubes and relays to silicon and integrated circuits, the size and cost of electronic components began to decrease. Electronics became more prevalent in consumer goods, and the pressure to reduce the size and manufacturing costs of electronic products drove manufacturers to look for better solutions.
The shops in that list I’ve either used myself, or I know someone who has used them. The classic way of sending a board layout to a manufacturer is by creating Gerber files from your design. But some (ex. OSH Parks) also accept KiCad files directly so that you don’t have to do any conversion. But the following steps are more or less the same, no matter what software you use. "For real implementation of these systems, there needs to be cost parity and strong governmental regulations in place," said Nguyen.
Through dynamic mechanical analysis, we find negligible catalyst loss, minimal changes in storage modulus and equivalent polymer backbone composition across multiple recycling cycles. This recycling process achieves 98% polymer recovery, 100% fibre recovery and 91% solvent recovery to create new vPCBs without performance degradation. Overall, this work paves the way for sustainability transitions in the electronics industry.
Comments
Post a Comment